Centrifugal Casting Gaskets
The centrifugal casting process uses molten metal to make tubes for many industrial applications. Seals for the end of the die cast are critical for the casting processes, so tube casting companies need the right material for centrifuge sealing.
What Is Centrifugal Casting?
The centrifugal casting process is casting high-alloy tubes following this process:
- The die cast is closed at both ends with a refractory seal and metal cap.
- The inside wall of the die cast is covered with refractory powder to prevent the molten metal from sticking and make it easier to remove the cast when the process is complete.
- The die cast is preheated with a gas flame and rotated on an axis at high speed to offset gravitational force.
- The molten metal is ladled into one end of the cast.
- Centrifugal force shapes the molten metal into the tube shape.
This process is best for long cylindrical parts that have a length longer than the outside diameter. The interior dimension of the die cast determines the part’s outer diameter, and the amount of molten metal poured into the cast determines the inner diameter.
Applications for Spun-Cast Tubes
Metal tubes made from centrifugal casting has several applications:
- Radiant heaters
- Roll shafts, such as furnace rolls and paper mill rolls
- Shipbuilding
- Oil and chemical
Discuss Your Molten Metal Project With McNeil Today
Centrifugal casting seals can handle the high temperatures and compression from centrifugal force. Reach out to us today to discuss your project or learn more.
Manufacturer’s Specifications
Click image to enlarge
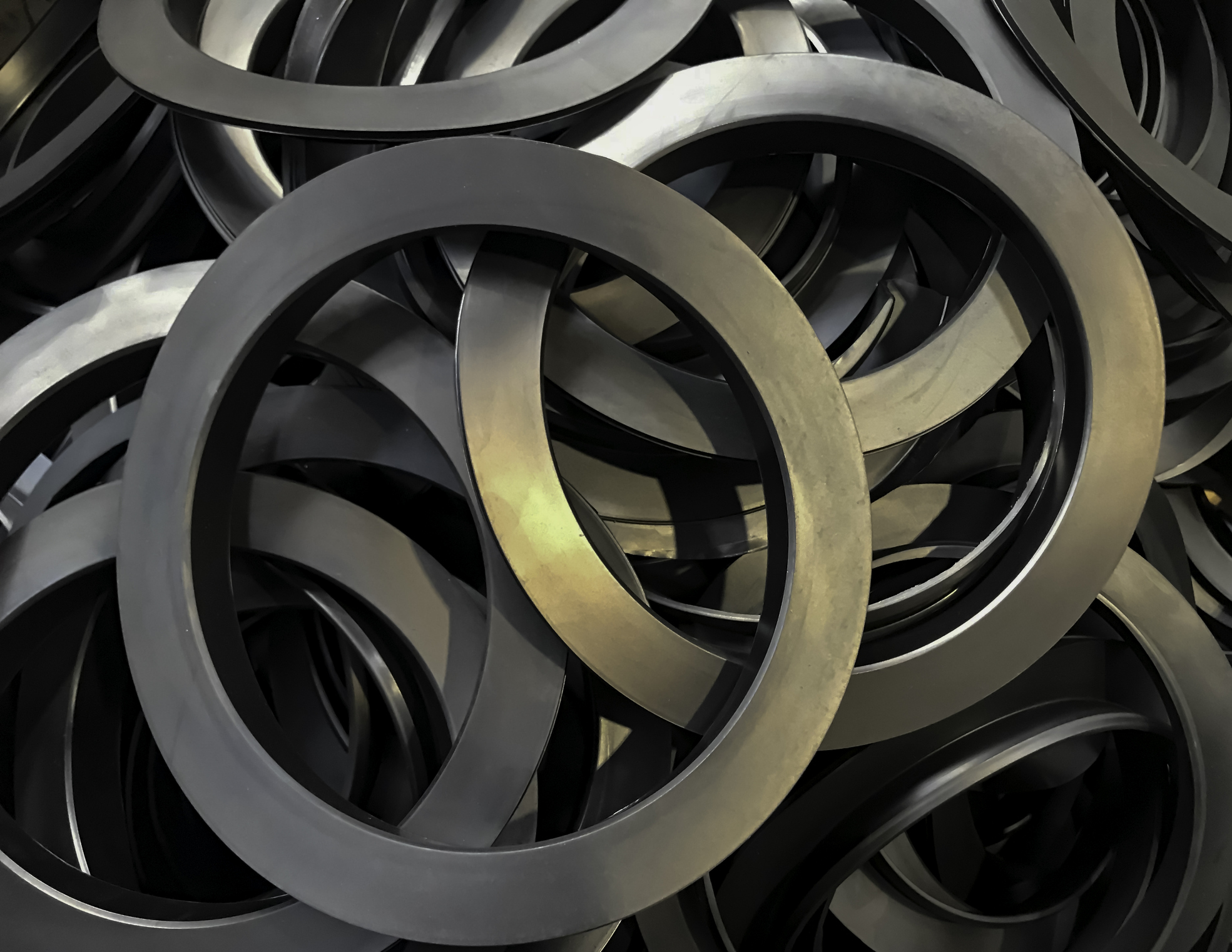